Understanding the Six Sigma Methodology for Quality
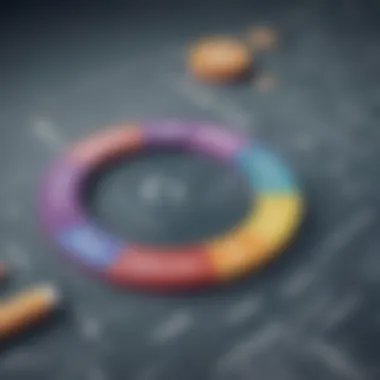
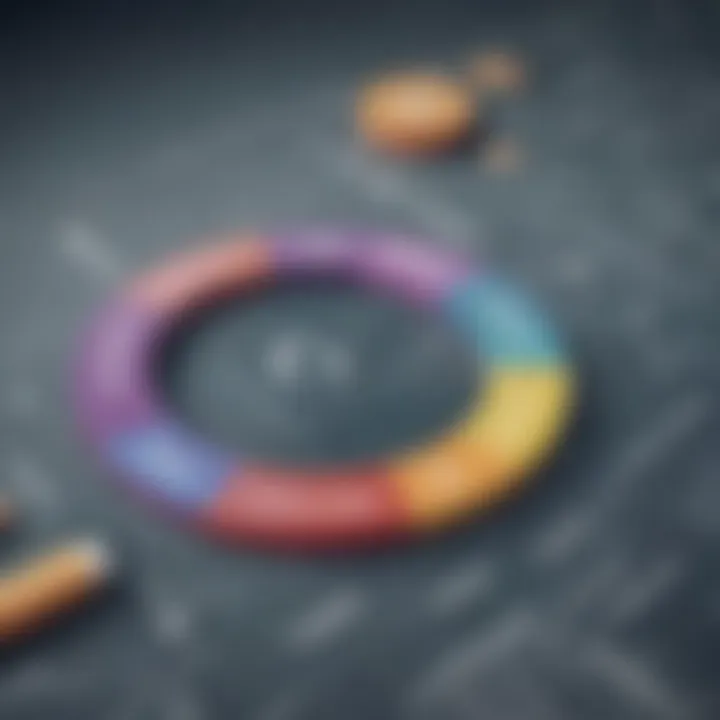
Intro
The evolution of modern industry relies heavily on methodologies that can optimize processes and enhance quality. This is where Six Sigma makes its mark. Originally developed by Motorola in the 1980s, Six Sigma has become a cornerstone for quality management and operational excellence across various sectors. It represents a disciplined, data-driven approach aimed at reducing defects and improving overall efficiency. While many might associate Six Sigma strictly with manufacturing, its principles have found practical applications in service sectors as well, from healthcare to finance.
Understanding Six Sigma is not merely about learning a set of tools; rather, it's about embracing a mindset fostering continual improvement. The following sections will delve deeper into the core aspects of Six Sigma, outlining its key principles, practical applications, and the statistical techniques that power its effectiveness.
Investment Terminology Breakdown
Although Six Sigma is not a financial concept per se, it employs terminologies that can be crucial for stakeholders investing in quality improvement processes. Grasping these terms enhances communication among peers and lays the groundwork for effective implementation. Here’s a breakdown of some common terms often encountered in the context of Six Sigma and quality management:
- Defect: Any instance where a product or service falls short of customer expectations.
- Process Capability: A statistical measure of the inherent variability of a process, indicating how well it can produce output consistently within specifications.
- Sigma Level: A measurement of process capability, with higher sigma levels indicating better quality and fewer defects.
Common Investment Terms Explained
Incorporating Six Sigma practices into an organization can resemble making strategic investments. Understanding these terminologies can empower decision-makers:
- ROI (Return on Investment): In the context of Six Sigma, it refers to the quantifiable benefits achieved through process improvements relative to the costs incurred during implementation.
- Cost of Quality: This includes all costs associated with ensuring good quality, including prevention, appraisal, and failure costs.
Understanding Financial Jargon
Navigating the world of finance demands clarity, much like working within a Six Sigma framework. The goal is to reduce ambiguity. Just as financial advisors avoid jargon with clients, leaders should strive for clarity in applying Six Sigma principles, ensuring every team member comprehends their role in the process.
"Quality means doing it right when no one is looking." - Henry Ford
Practical Application of Six Sigma
Six Sigma is not just about reducing defects; it's about creating a culture of excellence that permeates throughout an organization. Its most recognized methodology is the DMAIC framework:
- Define: Identify the problem or opportunity for improvement and define project goals.
- Measure: Collect data to understand how the process currently operates.
- Analyze: Investigate data and determine root causes of defects.
- Improve: Develop solutions to eliminate root causes.
- Control: Implement monitoring systems to sustain improvements.
Finale
In the overarching narrative of business excellence, Six Sigma plays a pivotal role, stitching together various aspects of quality management into a coherent strategy. It empowers businesses to refine processes, ensuring that they not only meet but exceed the expectations of customers—an invaluable asset in today’s competitive landscape. Understanding Six Sigma is more than an academic exercise; it represents a transformative journey towards operational excellence.
Preamble to Six Sigma
The realm of quality management is crucial for companies striving for excellence in processes and products. Here enters the Six Sigma methodology, a disciplined and data-driven approach designed to enhance operational effectiveness and minimize errors. The importance of the topic Introduction to Six Sigma lies in its ability to instill a culture of continuous improvement within organizations. This approach not only seeks to refine processes but also elevates customer satisfaction and can lead to significant cost savings.
In an increasingly competitive landscape, understanding Six Sigma becomes imperative. Investors, financial advisors, and accountants alike can gain insightful perspectives on the methodologies that drive efficient operations. Companies more effectively utilizing Six Sigma frameworks can often boast improved Bottom Lines. By understanding this concept, professionals can engage in more informed discussions about potential investments or strategies in various sectors.
Defining Six Sigma
Six Sigma is often defined as a set of techniques and tools aimed at process improvement. Originating from the manufacturing sector, it has evolved to apply to various industries, transforming productivity and operational effectiveness. The term "Six Sigma" derives from the statistical concept of process variation, specifically the idea of limiting defects to fewer than 3.4 per million opportunities. This high standard of quality signifies not just perfection but also a keen attention to reducing errors in every business aspect.
At its core, Six Sigma encompasses a variety of strategies, including what is known as the DMAIC framework: Define, Measure, Analyze, Improve, and Control. By focusing on these stages, organizations can systematically enhance their processes and overcome defects and inconsistencies. The primary goal remains to maintain quality at every step, thus ensuring that the output consistently meets or exceeds customer requirements.
Historical Context
The inception of Six Sigma traces back to the 1980s at Motorola, where the need to improve product quality became paramount. By harnessing statistical methods, the company was keen on achieving lower defect rates. With a commitment to quality assurance, Motorola set the stage for a broader application of these methodologies across various industries. The success story didn't stop there; companies like General Electric adopted Six Sigma during the 1990s, further validating its effectiveness and providing a blueprint for success.
Interestingly, this journey highlights a cultural shift from reactive quality measures to proactive management methodologies. Instead of waiting to catch defects after they occur, Six Sigma promotes the idea of building quality into processes from the get-go. This historical context emphasizes how Six Sigma evolved from a mere concept into a vital element of modern quality management practices.
"Quality is everyone's responsibility." - an adage that reflects the essence of Six Sigma's inclusive approach.
Core Principles of Six Sigma
At the heart of Six Sigma lies a set of core principles that are crucial to its effectiveness in driving quality improvement and efficiency. These principles shape the framework through which organizations strategize their processes and engage with customers. Understanding these core components is essential not only for those involved in quality management but also for investors, financial advisors, or any decision-makers invested in ensuring the operational excellence of their organizations.
The efficacy of Six Sigma hinges on these guiding principles:
- Focus on the Customer
- Data-Driven Decision Making
- Process Improvement
Each of these elements stands on its own, yet they interconnect to create a comprehensive strategy for reducing defects and enhancing overall performance. Let's delve deeper into these components.
Focus on the Customer
One of the staunchest principles of Six Sigma is ensuring that customer requirements are the cornerstone of all improvement efforts. It is not just about meeting customer expectations but exceeding them. This heightened focus means understanding customer needs, preferences, and how they perceive quality. Incorporating the voice of the customer into every aspect of the process can guide the team to make better decisions.
In practice, this might involve:
- Conducting surveys to gather direct feedback.
- Analyzing complaint data to identify areas needing attention.
- Constantly benchmarking service delivery against competitors.
Emphasizing a customer-centric approach not only builds loyalty but can significantly enhance market reputation, thus contributing positively to the overall bottom line. If quality and customer satisfaction take center stage, the ripple effects could resonate strongly within profit margins and customer retention rates.
Data-Driven Decision Making
Gone are the days when business decisions could rely on gut feelings or anecdotal evidence. In Six Sigma, data reign supreme. This principle emphasizes the need for rigorous statistical analysis and quantitative data to inform decision-making processes. The rationale behind this approach is simple: data is objective, and using it as a compass can steer an organization toward achieving its quality goals more effectively.
The implications of data-driven strategies include:
- Enhanced accuracy in predicting process trends.
- Identification of actionable insights that may not be visible on the surface.
- Informed, confident decision-making that minimizes risk and uncertainty.
Utilizing tools such as control charts, histograms, and regression analysis allows practitioners to visualize data patterns and drive continuous improvement. Integrating such disciplined methodologies ensures processes are optimized based on factual evidence rather than subjective perceptions.
Process Improvement
At its core, Six Sigma is synonymous with process improvement. The philosophy posits that in almost every business environment, there are inefficiencies and defects that, if addressed, can be transformed into opportunities. Focusing on refining processes can yield dual benefits: reducing error rates and improving overall productivity.
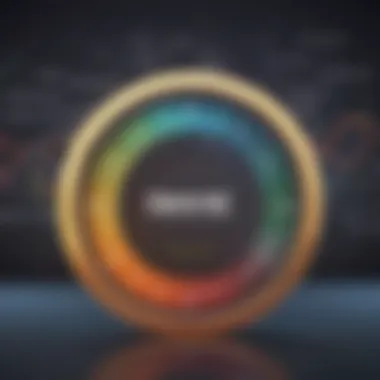
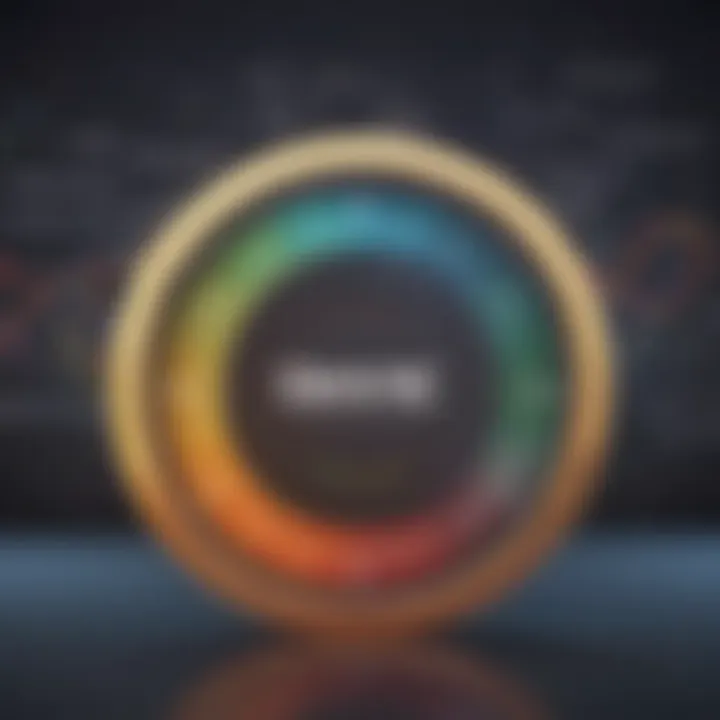
In practice, successful process improvement is achieved through:
- Mapping current processes to identify bottlenecks or waste.
- Engaging team members in brainstorming sessions to solicit input on potential improvements.
- Testing pilot solutions before full-scale implementation to gauge effectiveness.
A commitment to continual enhancement does not simply create a faster operation; it cultivates a culture of excellence. Each iteration ideally leads to a better, leaner process that ultimately delivers increased value to customers while lowering operational costs.
"An organization that embraces the core principles of Six Sigma can transform not just its processes but its entire culture."
The DMAIC Process
The DMAIC process stands as a cornerstone of Six Sigma. It is a structured approach that guides teams through a cycle of continuous improvement. By following the DMAIC framework, organizations can systematically tackle problems, reduce variability, and enhance processes. Here’s why understanding each phase of DMAIC is imperative for any professional looking to implement Six Sigma effectively.
Define Phase
In the Define phase, the focus is on identifying the problem or improvement opportunity clearly. Here, stakeholders gather to articulate the goals of the project. It usually involves defining the project scope, securing support from management, and understanding customer needs.
Key elements include:
- Project Charter: A document that formally outlines the objectives and scope.
- Voice of the Customer (VoC): Capturing customer requirements ensures that the solutions addressed during the project align with what the customer values.
By rigorously defining the project, organizations can avoid scope creep and enhance focus, leading to better outcomes.
Measure Phase
The Measure phase is where the rubber meets the road. It involves collecting data to understand current performance concerning the defined problem. This phase is crucial because without accurate data, it’s tough to gauge how effectively the processes are functioning.
Important actions in this phase include:
- Key Performance Indicators (KPIs): These metrics help track progress objectively.
- Baseline Measurements: Establishing a baseline for performance provides a reference point for future comparison.
- Data Collection Plan: Creating a systematic approach for gathering relevant data ensures consistency and reliability.
With reliable data, teams can move confidently into the next phase, setting the stage for meaningful analysis.
Analyze Phase
In the Analyze phase, the goal is to identify root causes of the problem. Teams scrutinize the data collected earlier to find patterns and correlations. Statistical tools are often employed here.
Some focus areas include:
- Cause-and-Effect Analysis: Tools like fishbone diagrams help visualize potential causes of problems.
- Statistical Testing: Determines whether observed variations are significant or merely noise.
This phase is where the adage "not all that glitters is gold" becomes relevant; it’s vital to delve deeper and distinguish the superficial from the actual drivers of issues.
Improve Phase
During the Improve phase, teams brainstorm solutions to the identified root causes. It's a moment of creativity and collaboration as stakeholders consider various options to enhance process performance.
Key elements in this phase include:
- Solution Development: A wide array of improvements are proposed, from changes in processes to adjustments in training.
- Pilot Testing: Before full-scale implementation, solutions should be piloted to evaluate effectiveness without committing extensive resources.
This stage is crucial because implementing changes without proper testing can lead to more issues down the line. Teams must be thorough and methodical.
Control Phase
The final segment is the Control phase, which aims to sustain the improvements achieved. This phase helps ensure that the gains made in the earlier steps are not just a flash in the pan.
Essential aspects of this phase include:
- Monitoring Plans: Establishing ongoing tracking of performance metrics keeps the improvements in check.
- Documentation: Clear documentation of procedures aids in maintaining consistency, especially with turnover or process changes.
After all the hard work, a robust Control phase can mean the difference between a project that sticks and one that flounders as soon as attention shifts away.
In summary, DMAIC is not merely a checklist. It's an interwoven series of steps that enhances operational effectiveness. Companies that adeptly employ this framework often find themselves not just surviving but thriving in their respective industries.
Statistical Tools in Six Sigma
Statistical tools are the backbone of the Six Sigma methodology. They are critical because they help identify trends, measure performance, and highlight areas ripe for improvement. By employing statistical techniques, teams can transform raw data into meaningful insights. This not only improves decision-making but also drives higher standards of quality and efficiency throughout an organization.
The application of statistical tools allows those who implement Six Sigma to demonstrate facts over feelings or assumptions. Numbers don’t lie, as they say. Decisions based on solid statistical evidence tend to yield better results, often leading to more significant improvements and innovations.
In the context of Six Sigma, three key statistical tools stand out:
- Quantitative Analysis Techniques
- Quality Control Charts
- Process Capability Analysis
Each holds unique value, and together, they compose a robust framework for quantifying performance.
Quantitative Analysis Techniques
Quantitative analysis techniques refer to various methods used to analyze numerical data. They play an important role in identifying issues in workflow, understanding variabilities, and predicting potential outcomes. Tools like regression analysis, hypothesis testing, and sampling distributions are common in this arena.
For example, let's say a manufacturer decides to explore the factors affecting their production line efficiency. They could utilize regression analysis to determine how variables such as machine speed, operator skill level, and raw material quality impact total output. By crunching the numbers, the team would find which factors carry the most weight and subsequently focus improvement efforts accordingly.
Quality Control Charts
Quality control charts are visual tools that track process behavior over time. They help in identifying trends, shifts, or any unexpected variations in production quality. A firm that produces automotive parts, for instance, could use control charts to monitor the defect rates. If the defect rate begins to trend upward, this visual indicator would alert management to investigate the cause, suggesting a potential adjustment in the production process might be necessary.
Quality control charts help teams analyze what's going right and wrong in their processes, allowing for data-driven adjustments when needed.
These charts provide a clear picture—like looking at the stars in a well-lit sky versus a cloudy night. They allow analysts to detect changes with ease so they can take action before issues spiral out of control.
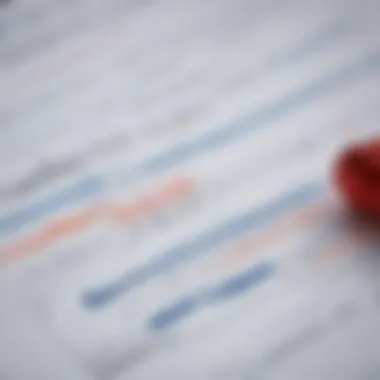
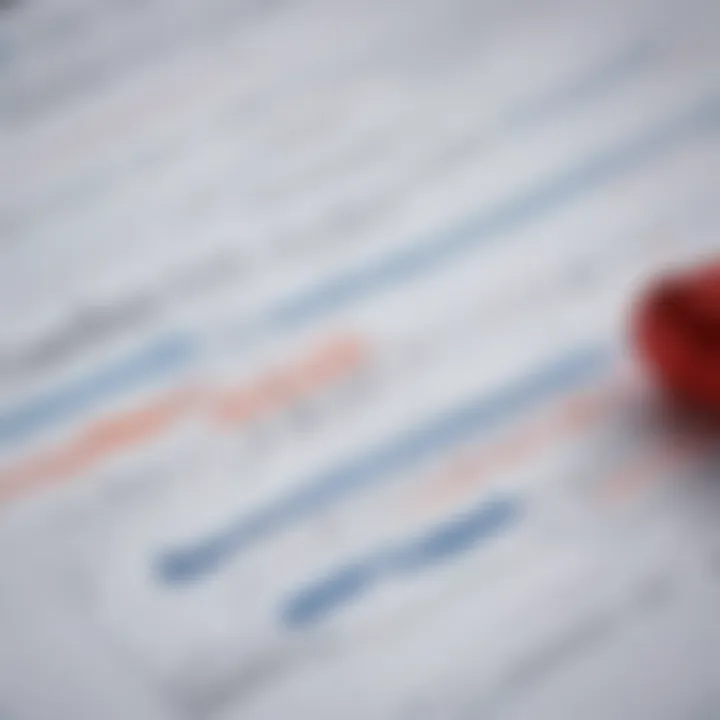
Process Capability Analysis
Process capability analysis evaluates how well a process meets specified performance standards. It’s all about aligning the process results with customer expectations. If a business knows that consumers are expecting certain dimensions in a product, they can use capability analysis to assess whether their production processes are capable of consistently meeting those specifications.
Consider a company manufacturing valves for industrial equipment. By analyzing the process capability, they might find they’re operating at a capability index (Cp) of 1.33, which indicates room for improvement as customers prefer an index of at least 1.67 for confidence in quality. This insight could lead to targeted actions that not only meet but potentially exceed customer requirements.
In summary, the application of these statistical tools within the Six Sigma framework is indispensable. They provide practical insights that lead to actionable improvements, ensuring that organizations remain competitive and responsive to market demands.
Application of Six Sigma
Understanding the application of Six Sigma offers valuable insights into its transformative potential across various industries. The methodology is not just limited to manufacturing but extends its reach into service sectors, ultimately influencing overall business performance. It equips organizations with tools and frameworks to improve processes, reduce costs, and enhance customer satisfaction. Let's delve into specific areas where Six Sigma is applied to reveal its practical significance.
Manufacturing Sector
In the manufacturing domain, Six Sigma serves as a linchpin for quality control and operational excellence. It's all about precision and reducing variability in processes, which directly translates into cost savings. Manufacturers utilize the DMAIC methodology to identify inefficiencies, leading to significant improvements.
When a company implements Six Sigma principles, they often experience the following benefits:
- Improved Quality: Reducing defects means that products meet customer expectations more consistently.
- Increased Efficiency: Streamlined processes lead to faster production cycles.
- Cost Reduction: Less waste means lower operational costs.
For instance, a automotive manufacturer might apply Six Sigma to its assembly line to pinpoint where defects occur in part assembly. By meticulously analyzing these processes, they can make targeted enhancements that eliminate waste and boost overall quality. The bottom line? A smoother operation that satisfies both the company’s financial goals and customers’ standards.
Service Sector
While many might think of Six Sigma as a tool for factories, its importance in the service sector is irrefutable. Organizations ranging from banks to hospitals have employed Six Sigma to refine their service delivery. By focusing on customer feedback and process mappings, businesses can enhance the customer experience significantly.
Key aspects of Six Sigma in service applications include:
- Reducing Wait Times: Banks can streamline their operations to cut down the time customers spend waiting in queues.
- Enhancing Accuracy: In healthcare, reducing errors in patient records can lead to better outcomes and increased trust.
For example, a healthcare facility might implement Six Sigma to tackle patient admission processes. Through data analysis, they could discover that certain administrative steps cause bottlenecks. Addressing these inefficiencies can lead to significant time savings and a better overall experience for patients, ultimately resulting in increased patient satisfaction and loyalty.
Case Studies
Real-world case studies illuminate the impact of Six Sigma in various fields. Companies that adopt this methodology often document their journeys, outlining both challenges and triumphs, thus providing a roadmap for others.
Here are a couple of notable examples:
- General Electric: GE's adoption of Six Sigma has become legendary in business circles. The firm reported savings in the billions as a result of its initiatives, executing projects aimed at reducing cycle times and improving product quality.
- Motorola: Motorola played a pivotal role in the creation of Six Sigma. They demonstrated drastic reductions in defects per million opportunities, leading to fantastic improvements in product integrity and customer satisfaction.
These case studies serve as testaments to Six Sigma's adaptability and effectiveness. They showcase how critical thinking combined with statistical tools can lead to tangible business improvements.
Applying Six Sigma is akin to finding the gears of a well-oiled machine; when each piece works in harmony, the overall system operates smoothly.
In summary, the application of Six Sigma transcends industry boundaries. Whether in manufacturing or services, the quest for quality and efficiency remains paramount. By studying successful implementations, organizations can draw lessons and strategies to fuel their own growth and improvement.
Benefits of Implementing Six Sigma
Implementing Six Sigma methodologies in organizations brings forth several tangible benefits. Understanding these advantages can shed light on the rationale behind businesses investing their time and resources into mastering this concept. Not only is it about improving processes; it is fundamentally about transforming organizational culture and driving results that resonate at every level.
Cost Reduction
One of the primary advantages of adopting Six Sigma is the potential for cost reduction. With its systematic approach to identifying faults and inefficiencies, organizations can significantly decrease waste. By applying tools such as value stream mapping, companies can identify non-value-added activities that drain resources. For instance, a manufacturing company might notice that long machine setups cause delays and lead to wasted materials. By reducing setup times with Six Sigma techniques, this company could save thousands, if not millions, annually, improving its bottom line.
Moreover, when defects are minimized, the costs associated with rework or recalls drop accordingly. Operational efficiency becomes the order of the day, and as agencies streamline their processes, they invariably lower their operational costs. This ability to cut costs while maintaining high quality is invaluable for any organization looking to sustain its competitive edge in an increasingly cutthroat market.
Increased Customer Satisfaction
In the world of business, customer satisfaction is king. Six Sigma plays a critical role in ensuring that a company meets or surpasses customer expectations. Through data-driven insights and rigorous analysis, firms can refine their outputs to achieve the highest quality. Picture a retail company that consistently receives complaints about delayed shipments. By implementing Six Sigma practices, such as optimizing their supply chain processes, the organization can significantly reduce lead times.
As a result, customers are pleased with faster deliveries, which often translates into repeat business and favorable word-of-mouth recommendations. Customers tend to stick around when they know they can rely on a brand. This increased loyalty isn't just a bonus; it transforms into steady revenue and profitability over time.
"Quality is everyone's job, not just the folks in the quality department."
Enhanced Employee Engagement
Implementing Six Sigma can also lead to enhanced employee engagement. Many organizations underestimate the impact that process improvement methodologies have on employees. When staff are involved in problem-solving and decision-making processes, their sense of ownership and pride in their work grows. In many cases, employees at various levels have hands-on insights into issues. Encouraging them to participate in Six Sigma projects not only hunts down inefficiencies but also boosts morale.
Employees who see that their suggestions are valued are more likely to feel motivated. Companies that promote such engagement often witness reduced turnover, increased productivity, and a more united team. Those benefits, in turn, lead to ongoing improvements in performance, creating a virtuous cycle of growth and success.
Investment in Six Sigma is not just a strategy to implement; it is an invitation to redefine how an organization operates. As businesses adopt this beneficial methodology, they find that the interplay of cost management, customer satisfaction, and employee engagement creates an environment conducive to innovation and resilience.
Challenges in Six Sigma Implementation
Implementing Six Sigma is not a walk in the park, and organizations often face numerous challenges when trying to integrate this methodology into their processes. This section delves into the various hurdles encountered during the implementation phase and emphasizes the significance of addressing these challenges to fully leverage the benefits of Six Sigma. Understanding these issues provides valuable insight on how firms can enhance their quality management efforts while navigating potential pitfalls.
Cultural Resistance
Cultural resistance stands as one of the most formidable challenges in Six Sigma implementation. When organizations attempt to introduce new processes and methods, employees may cling to the traditional ways of doing things. This reluctance often comes from a fear of change or uncertainty about how these new practices will affect their roles within the company.
Moreover, if the organizational culture does not promote continuous improvement or data-driven decision-making, it can be downright uphill. Employees may perceive Six Sigma as a top-down initiative rather than a collaborative effort. Therefore, leaders must create an environment that encourages participation and fosters openness to change. This can be achieved through:
- Organizing workshops to educate employees on Six Sigma principles.
- Encouraging feedback and addressing concerns.
- Recognizing and rewarding contributions to improvement efforts.
Addressing cultural resistance early on not only helps in smoother implementation but can also enhance morale and engagement among staff, making them feel like active participants in the process.
Sustaining Improvements
The next significant challenge revolves around sustaining the improvements brought by Six Sigma. Many organizations report initial success, only to see performance declines over time as focus wanes.
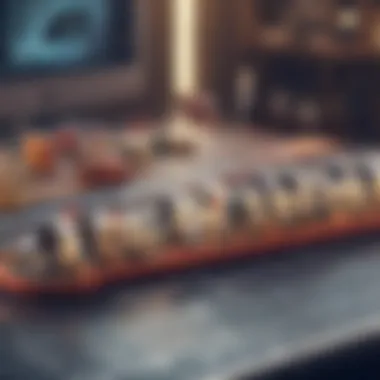
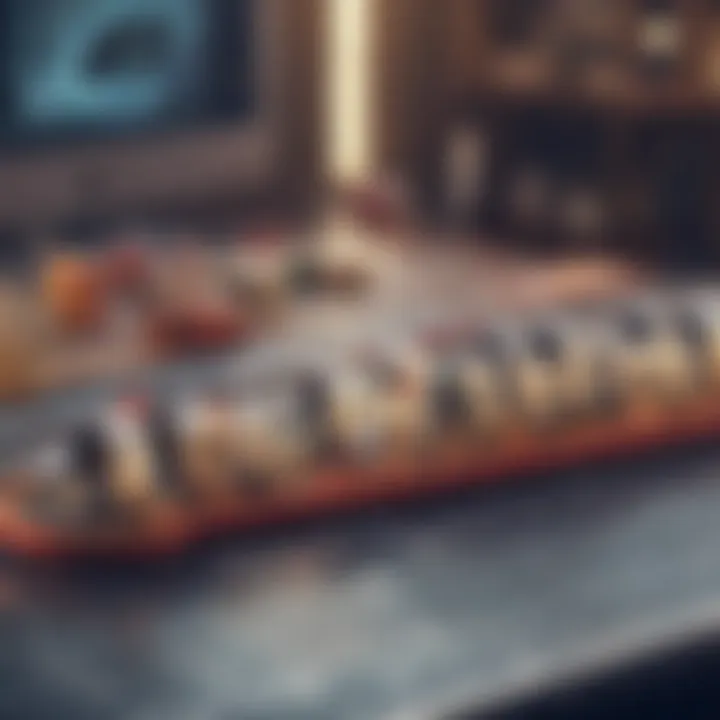
Sustaining these improvements requires persistent effort and commitment from all levels of the organization. It's not just a matter of implementing new processes; it’s about embedding a mindset of continuous improvement into the company’s DNA. Some effective strategies include:
- Establishing regular reviews to track progress and reinforce goals.
- Providing ongoing training and support for employees involved in Six Sigma projects to ensure skills remain sharp.
- Creating a Six Sigma council to oversee initiatives, facilitate communication, and encourage interdisciplinary collaboration.
These steps ensure that the momentum built during initial Six Sigma initiatives does not wane and that the organization remains committed to maintaining high standards of quality and performance.
Resource Allocation
Another critical area of concern in the implementation of Six Sigma relates to resource allocation. Effective implementation demands not just human resources but also financial investment, time, and tools. Often, companies underestimate the allocation required to set up Six Sigma processes effectively.
To avoid the pitfalls that come from misallocated or insufficient resources, organizations should:
- Conduct a thorough assessment of necessary resources before initiating Six Sigma projects, from personnel to technology.
- Prioritize projects that align best with strategic goals to ensure that they are not spread too thin.
- Foster collaboration among departments to optimize shared resources, thus enhancing the overall effectiveness of Six Sigma initiatives.
Without adequate resources, Six Sigma efforts may flounder, resulting in lost productivity and wasted potential. Managing resource allocation smartly not only supports immediate goals but also establishes a strong foundation for long-term success.
"In a world that's constantly changing, the only way to stay ahead is through continuous improvement and adaptation."
By acknowledging and addressing these challenges, organizations can pave the way for successful Six Sigma implementations that yield tangible benefits for quality management.
Six Sigma Certifications
Six Sigma certification plays a pivotal role in helping organizations adopt the Six Sigma methodology effectively. This certification is not merely a badge one wears; it signifies a proven understanding of quality management principles, structured problem-solving, and the ability to minimize defects within processes. For investors, financial advisors, and accountants, grasping the relevance of these certifications is vital because they directly correlate with enhanced operational efficiency and cost management—elements that can shape the profitability of businesses they are involved with.
The significance of Six Sigma certifications can be broken down into several components:
- Professional Growth: Obtaining a Six Sigma certification positions professionals at an advantage in the job market. It displays expertise that is recognized globally and is often sought after by employers looking for leaders in quality improvement.
- Organizational Value: Trained professionals can lead projects that eliminate waste, cut costs, and improve quality. This, in turn, attracts investors who recognize a company’s commitment to operational excellence.
- Skill Development: As practitioners navigate through the intricacies of Six Sigma, they develop a plethora of skills—analytical thinking, project management, and cross-functional team collaboration. Skills that are tremendously valuable in any organizational setting.
"Quality is never an accident; it is always the result of intelligent effort." — John Ruskin
Belt System Overview
The Six Sigma belt system is essential in categorizing the levels of expertise among practitioners. Each belt level represents a different degree of knowledge, experience, and responsibility, and here’s how it typically breaks down:
- White Belt: A basic understanding of Six Sigma principles, often used for introductory training, enabling employees to grasp fundamental concepts.
- Yellow Belt: These individuals have a deeper understanding and may assist in project teams. They actively participate and contribute to projects in limited roles.
- Green Belt: More knowledgeable and skilled staff, Green Belts manage smaller projects and assist Black Belts on larger projects. They are usually the backbone of Six Sigma initiatives.
- Black Belt: Specializes in Six Sigma methodologies. They lead and manage projects, provide mentorship to Green and Yellow Belts, and carry a significant responsibility for implementing large-scale improvements.
- Master Black Belt: At this highest tier, individuals mentor Black Belts and guide organizational strategy, focusing on large-scale initiatives and training new professionals.
Importance of Certification
Why should professionals and organizations invest in Six Sigma certification? The advantages extend beyond personal achievement:
- Credibility: A certification assures stakeholders of an individual's commitment to quality and efficiency, making it easier to gain trust in a business environment.
- Framework for Success: Learning the intricacies of Six Sigma allows practitioners to utilize proven frameworks like DMAIC effectively, increasing the probability of successful project outcomes.
- Informed Decision-Making: With the deep statistical knowledge gained through certification, professionals are positioned to make informed and data-driven decisions that resonate with best practices.
- Strategic Advantage: Having certified personnel in-house can provide a competitive edge. Organizations become more agile in adapting to market changes and are better equipped to respond to client needs.
In summary, Six Sigma certifications not only fuel individual careers but also enhance the operational capacity of organizations as a whole. For investors and financial professionals, recognizing the value of this certification within a corporation can be a crucial factor in decision-making processes.
Future Trends in Six Sigma
As Six Sigma continues to evolve, understanding its future trends is crucial for organizations aiming to maintain a competitive edge. The landscape surrounding quality management is rapidly changing, influenced by new methodologies and technological innovations. Embracing these trends not only enhances operational efficiency but also fosters a culture of continuous improvement.
Integration with Lean Practices
The concept of Lean, focused on eliminating waste while maximizing customer value, is increasingly converging with Six Sigma principles. This integration leads to the development of Lean Six Sigma, a potent methodology that combines the strengths of both frameworks.
By fusing these approaches, organizations can streamline processes significantly. For instance, a manufacturing plant aiming to reduce cycle times while improving product quality could utilize the Lean Six Sigma approach. This dual strategy enhances flexibility, ensures quicker response times, and ultimately, delivers better results.
Moreover, Lean Six Sigma provides a comprehensive toolkit for organizations, encouraging:
- Continuous process evaluation
- Enhanced employee engagement in quality initiatives
- Improved problem-solving capabilities
- Greater alignment of projects with strategic goals
In this increasingly competitive market, businesses that embrace the integration of Lean and Six Sigma are more likely to achieve sustainable improvements and see tangible gains in their bottom line.
Technological Advancements
Technology plays a pivotal role in shaping the future of Six Sigma. With the advent of big data and advanced analytics, organizations have access to a wealth of information that can be leveraged for more informed decision-making. Today, businesses can analyze massive amounts of data with precision, identifying patterns and trends that were previously difficult to discern.
For example, predictive analytics enables companies to anticipate future defects in manufacturing processes. By implementing data visualization tools and machine learning algorithms, organizations can proactively address quality issues before they escalate. This shift toward a data-centric approach helps organizations in:
- Streamlining processes with real-time data
- Enhancing quality control with predictive models
- Reducing costs through informed resource allocation
Additionally, automation tools can effectively minimize human error, which traditionally hampers Six Sigma initiatives. Implementing robotic process automation (RPA) can lead to significant improvements in efficiency, allowing teams to focus on more strategic quality improvement efforts.
"The integration of technology in Six Sigma practices transforms traditional quality management into a proactive strategy that can adapt to rapid changes in the business environment."
Embracing technological advancements not only strengthens Six Sigma applications but also reinforces a commitment to quality excellence.
In summary, the future of Six Sigma is bright, marked by the integration of Lean principles and technological innovations. Businesses that stay ahead of these trends will not only improve their operational processes but also ensure they remain agile in a dynamic market.
Epilogue
The concept of Six Sigma offers a structured methodology that transforms how organizations pursue quality and efficiency. By utilizing data-backed insights to minimize variability and enhance process performance, Six Sigma plays a pivotal role in driving operational excellence.
Recap of Key Points
To recap the essence of Six Sigma, it's organized around several core elements:
- Customer Focus: Understanding and meeting customer needs is at the heart of Six Sigma. Ensuring that the output corresponds to customer expectations not only retains customer loyalty but also enhances the organization's reputation.
- Data-Driven Approach: The reliance on statistical analysis aids in identifying defects and inefficiencies. Organizations can make informed decisions rather than relying on guesswork.
- Continuous Improvement: By engaging in a cycle of defining, measuring, analyzing, improving, and controlling, organizations embed a culture of ongoing enhancement into their daily operations.
Implementing these principles can lead to significant cost reduction, higher customer satisfaction, and improved employee engagement, making it a comprehensive solution for both manufacturing and service industries.
Final Thoughts
Six Sigma is not just a series of techniques; it's a philosophy that, when integrated into an organization's culture, can yield transformative results. The benefits extend beyond mere numbers; it enhances collaboration, fosters a sense of ownership among employees, and drives strategic alignment.
Organizations embarking on a Six Sigma journey should approach it with an open mind. Challenges, like cultural resistance, may arise, but with perseverance, the long-term gains far outweigh the temporary hurdles. As we are witnessing an increasing integration of technological advancements, Six Sigma continues to evolve, perpetuating its relevance in modern business practices.
In light of this comprehensive understanding, it is clear that Six Sigma will continue to be a vital tool for professionals aiming for excellence in their respective fields.